摘要:漳泽发电厂#1汽轮机由于生产年代较早,投入运行时间长,存在许多缺陷,同时机组经济效益低下、热耗率过高。通过对机组通流部分现代化改造及调速系统DEH改造,消除了设备隐患。改造后提高了机组出力和使用寿命,节能降耗,经济效益显著。
关键词:汽轮机 通流部分 设备改造 经济分析
1 机组存在的问题
漳泽发电厂#1汽轮机采用原苏联50年代技术设计生产的产品,与现代设计制造水平相比,其设计理论落后、生产制造水平低,主要表现为热力特性差、结构设计较为落后、汽轮机效率低、能耗大、电厂经济性较差,同时由于机组出厂已27年,设备上存在许多重大缺陷,需要利用大修彻底消除,具体表现如下:
1.1 汽缸漏汽、调门汽室群裂
高压缸漏汽可以追溯到1999年底,一次甩负荷后,出现缸高压侧猫爪开始漏汽,虽漏汽量不是很大,但站在前箱处,可以感到明显汽流,尤其在启停机,汽缸法加系统投运时,漏汽量更加明显。为此在机组正常运行中,只能稍开法加至凝汽器门,以引走大部从汽缸中窜的蒸汽,这样做会使凝汽器的冷汽对高缸产生冲击,使汽缸结合面出现冷热应力,加速汽缸裂纹的出现。
在1993年8月大修时发现,高压缸下半左侧蒸汽室内存在较为严重的群裂现象,当时采用挖补消除裂纹。在1997年12月大修时发现,高压缸下半左侧蒸汽室内又出现严重的群裂现象,高压缸上半左侧蒸汽室内也同样存在很多微裂纹,为此采用大面积挖补的办法除去大部裂纹,由于微裂纹很多,位置狭小,无法进一步打磨,当时未做彻底处理,给机组安全运行带来隐患。
1.2 不合格动叶片的存在
低压转子末级叶片曾多次发生断裂、裂纹。1987年6月首次大修时第20级叶片裂7片,裂纹均在外拉筋孔处,从内弧孔边沿开始向进汽边沿伸,裂纹长度为15-20mm,其中#3叶片已裂透。1993年8月大修时第20级叶片裂7片, 1997年12月大修时又发现第20级叶片裂3片。机组每次大修均需要进行更换低压转子叶片,不但增大了大修工作量,而且对机组长期安全运行带来极大隐患。
在2002年底至2003年初的跨年度大修时,发现低压第16级转子进汽侧轮盘根部燕尾槽3/4圈开裂,若非大修停机,可能会发生第16级转子叶片或轮盘飞出事故,后果不堪设想。
1.3 #1瓦球面吃力差,轴向位移超标
1997年大修时发现,#1瓦球面吃力非常差,球面、瓦枕变形严重,球面与瓦枕之间局部间隙达0.10mm,经磨削上瓦枕结合面后,接触点仅分布在球面下部及顶部,左右两侧间隙仍有0.10mm无法消除,整个球面接触点仅有40%左右,导致开机后,轴向位移经常在+0.95~+1.05mm(标准为-0.40~+1.00mm,报警值-0.40mm,+1.00mm,严重困扰机组的正常运转。
1.4 #6瓦垂直、水平振动大
#1机6瓦2002年9月20日轴向振动达90μm,水平振动达60μm。检查发现#6瓦底座及台板振动大,后采取临时措施,在下部备垫铁,并做支撑加固,使6瓦轴向振动在60μm,水平振动45μm,困扰机组安全运行。
1.5 经济效率低下,能源浪费严重
限于当时制造、设计条件,机组的热耗率非常高。从2002年大修前节能诊断试验结果来看,在100MW工况下的机组试验热耗率较设计值高7.55%,高、低压缸效率分别为84.6%、71.93%,比设计值偏低1.87%、8.07%。总之#1机组的经济指标不仅远低于目前同类新机组,并且与其设计值相比,也有很大差距,而且随着时间推移,机组主要部件老化严重,只有对设备进行改造,降低生产成本,提高设备完好率,才能在电力市场的激烈竞争中站稳脚跟。
2 影响机组经济性的主要因素
造成汽轮机组热耗偏高、缸效率偏低的原因是多方面的,高压缸设计比先进水平低约3-5%,低压缸效率也明显偏低。其主要原因为:设计落后,调速级效率偏低;静叶片未采用现代高效化设计,叶型损失和流动损失大;动叶片未采用可控涡优化设计,短叶片多为等截面直叶片,动叶损失大;围带和汽封结构不合理,叶栅拉筋过多,相对栅距不合理,通流的子午面不光滑;进汽和排汽通道压力损失大。同时由于制造工艺落后,安装检修有关间隙调整不当,使部分老机组实际内效率与设计值又存在较大偏差;加之汽缸结构不合理,汽缸内漏与本体相连的辅助系统泄漏,对主机经济性也产生很大影响。
3 改造技术方案
3.1 高压部分
⑴调节级由双列改为单列调节级,静叶采用子午面收缩型,高压压力级由原来14级增至15级。
⑵高压2~16级静叶采用高效"后加载"叶型,第2、3两级采用分流叶栅,第9~16级采用弯扭静叶栅。
⑶高压第2~16级动叶型线优化,全部采用自带冠成组或整圈联接。
⑷通流子午面光顺,取消全部拉筋,将原铸铁隔板改为焊接钢隔板。
⑸高压缸前部材料采用ZG20CrMoV,后部材料采用ZG230-450,并采用高窄法兰形式,取消法兰螺栓加热系统。
⑹高压转子采用整锻转子,材料为30Cr1Mo1V,增大过渡圆角。
⑺取消凸轮配汽机构,对调速系统实施DEH改造,实现每个油动机控制一个主汽门及调门。
3.2 低压部分
⑴适当提高根径,优化速比。
⑵低压第1~5级静叶采用高效"后加载"叶型,弯扭静叶。
⑶低压第1~5级动叶采用性能优良高效新叶型,全部自带冠,叶顶汽封齿数增为第1~4级4道,末级3道。
⑷末级叶片材料采用17-4PH加镶焊司太林合金,并设置疏水槽,提高抗水蚀性能。
⑸末级叶片根部反动度提高到25% 。
⑹原隔板改为焊接钢隔板;低压缸汽封采用斜平齿结构。
⑺通流子午面光顺,只保留末级一根拉筋,其它拉筋全部取消。
3.3 轴瓦
将#1-5瓦原三油楔轴瓦改为椭圆瓦,将#6瓦同时更换为新椭圆瓦。
4 设备安装及存在问题分析、解决
4.1 #6瓦水平、轴向振动大处理
经大修解体检查发现,六瓦台板与其下部垫铁未焊接固定,仅用混凝土浇筑固定。经过长时间运行,台板与垫铁之间松动导致机组运行时#6轴向振动达90μm,水平振动达60μm。在本次#1机大修中,把台板吊出,底部垫铁重新进行了更换、进行对研磨,并进行了段焊固定;对台板进行了清理,台板地脚螺丝进行了紧固、螺帽进行了点焊,找平找正后重新进行了二次浇灌。开机后6瓦的垂直、水平振动均小于20μm,轴向振动小于30μm。
4.2 前箱与台板间隙大处理
解体前箱后测量发现,前箱与台板之间接触非常差,前箱出现较大变形,间隙最大处达0.55mm,大部间隙在0.30-0.40 mm,通过刮研台板,并进行对研,总计将前箱底面刮去0.60mm,修理后两者接触点、接触面达到质量标准。为保证大修后前箱膨胀自如,采用东方汽轮机厂的石墨涂膜技术,在前箱及台板上涂润滑膜,保证了机组的正常膨胀。
4.3 大修中的质量把关
旧汽缸拆除前的测量数据是新汽缸安装、管道对口的依据,在改造中制定详细的施工方案,严格按施工工艺施工,派专人将新旧汽缸每个孔洞的规格、相对位置都做细致的测量、比较,保证了新汽缸的准确就位、各连接管道的正确对口。保证开机后汽缸及其所属管道无一处泄漏,机组真空严密性达到0.22MPa/min。
4.4 调门顶部抗燃油油缸直径过小,提升力不足处理
在#1机组改造时高低压通流部分供货(不含调门关闭器及油缸)、调速系统的DEH供货(含调门关闭器及油缸)及改造分别由两制造厂进行。
大修结束开机后发现,在主汽压力为4.0MPa左右,转速仅能上升至400rpm左右,调门开度维持在12-14%,(调门总行程40mm,预启阀行程4-5mm),调速汽门顶部抗燃油油缸提升力仅能开启预启阀,而不能开启调门阀体,为此被迫采取将EH油压由额定14.0MPa调高至15.2MPa,并采用主闸旁路门调整进汽方式,方能正常冲车。#1机组于2003年2月大修结束并网后,各调门摆动幅度大,负荷不稳,给设备安全运行造成威胁。
4.4.1 油动机提升力特性计算
DEH改造后各调门由各自的油动机控制,油动机采用单侧进油方式,油动机靠电液转换器控制油压开启,在机组正常运行状态,油动机的提升力与操纵座弹簧的作用力、阀门蒸汽力、摩擦阻力、部件重力平衡。当操纵座与油动机作为一个整体考虑时,油缸的有效提升力应为油缸的液力与操纵座弹簧的作用力的差值,由下列关系式可确定出油缸的有效提升力。
油缸有效面积: Sy=(D02- d02)×π/4
油缸提升力:Ft= Sy×Pk
油缸有效提升力:Fty = Ft-Fh
在油动机下油压达到抗燃油压供油压力时,油动机的提升力最大,而在调门启始状态时,弹簧的作用力最小,最大提升力与最小弹簧作用力Fh的差值为最大的有效提升力。选择不同的不同抗燃油压及油缸直径,就可确定油缸最大有效提升力与油缸直径的关系。
计算结果表明:提高抗燃油压可在一定范围内增加油动机的有效提升力会有所增加,DEH改造后的油缸直径为83mm,在抗燃油压由14MPa提高到15.5MPa时,有效提升力可提高530 kg,但提高油压会增加泵的出力,加速各密封胶圈的老化,易造成抗燃油管弯头漏油;而加大油缸直径对提高提升力作用明显,当油缸直径由83mm增加至102mm时有效提升力可提高一倍。
4.4.2 调门设计提升力问题的分析
原设计的调门预启阀通汽面积为4×φ4mm的小孔,在考虑门杆漏汽量的情况下,在阀套总间隙0.50mm时,阀体上部压力必须达到6.7MPa时,才能使阀套的漏汽量与小孔的排汽量平衡,此时调门需要的提升力为7.66t。原设计油缸直径为φ83mm,在油压为14-15.5MPa下的提升力范围为3.62-4.15 t,远不能适应调门提升力的需要。即使在油缸直径为φ102mm时,提升力范围也仅为7.88-8.55 t/h,不能满足调门提升力的需要,在不考虑门杆强度问题的情况下进一步加大油缸的直径,可满足其提升力的要求。
计算表明:在通汽孔为4×φ7mm时,当阀前后差压为500kPa时,在阀套总间隙为0.50mm情况下,阀芯前后差压为27kPa;间隙为0.40mm情况下,阀芯前后差压降至10kPa;而间隙为0.60mm情况下,阀芯前后差压增加至65kPa。因此阀套间隙变化对阀体的稳定性具有十分明显的影响。
加大阀体上部通汽面积,虽然可有效降低阀体上部压力,但加大上部通汽面积会明显降低阀体上部压力,可能会出现调门接近全开时产生调门不稳定摆动问题。
4.4.3 调门改进的最终方案、实施
通过对调门大开度下的稳定性分析、不同条件下调门阀芯前后差压计算、阀芯前后差压与阀前后差压的关系、阀套间隙变化对阀芯前后差压与阀前后差压关系的影响、调门门杆强度核算、调门关闭时间与油缸容积的关系等诸多因素的全面分析计算、对通汽孔打孔的比选,得出以下计算结论:
1)根据调门动态特性满足甩负荷动态特性、油动机提升力应有足够的富裕的要求及制造厂家现有油缸规范,选择改进后的油动机油缸直径φ102mm。
2)根据图纸及大修时测量,阀套总间隙为0.40 mm左右,由此选取调门预启阀通汽孔为4×φ7mm,门体不加补汽孔。
经计算调门开启所需最大提升力4.5t,油动机提升力达7.5 t以上,富裕量充足,并可保证1#、2#调门在大开度下,调门不会发生摆动问题。
在2003年6月17日-25日进行的小修中对调门预启阀通汽孔改进,由原来4-Ф4,改为4-Ф6.9;对调门油动机油缸由原83mm改为Ф102mm,原调门关闭器、油管、卸荷阀等未做改动。
开机试验证明,各调门关闭时间在0.15-0.24s之间,在各负荷点调门控制稳定,在极热态情况下调门主汽门可以顺利开启,改造取得了圆满成功。
5 改造效果及经济分析
5.1 保证工况的机组热耗率
试验证明,保证工况(三阀全开、第四阀解列)参数修正后的热耗率为8927.48kJ/kWh,经系统、参数修正后的最终热耗率平均值为8840.75 kJ/kWh,比厂家的合同规定值8855.08 kJ/kWh低14.33 kJ/kWh,达到了厂家改造合同的保证值。
5.2 保证工况机组的电功率
保证工况下、参数修正后的发电机功率平均值为105901.75kW,对应的主蒸汽流量为377.0925t/h,修正至额定主蒸汽流量392t/h时机组的发电机功率为110088.3kW,达到了合同保证值。
5.3 保证工况的缸效率
保证工况试验高压缸效率为87.19%,比设计值87.50%低0.31个百分点,低压缸修正后的平均效率为83.63%,比设计值84.20%低0.57百分点。
5.4 机组的最大连续出力及通流能力
#1机组通流部分改造后在最大负荷工况下的试验主蒸汽流量为401.13t/h,试验发电机功率为111203.8kW,修正后的主蒸汽流量为388.33t/h,修正后的发电机功率为109029.5 kW,将主蒸汽流量折算到厂家最大连续出力的设计流量414t/h时,发电机的功率为116237.9 kW,达到了厂家的最大连续出力115491 kW 。
5.5 机组各运行工况试验结果
本次试验还进行了105MW、95MW、85MW、80MW四个负荷工况试验。从总体趋势上看,试验结果的规律性很好。高负荷工况下,机组的热耗率随负荷的变化较为平缓。
测试数据表明,机组在110MW负荷运行时,发电机的主要技术参数无明显超标现象,且机组在最大工况运行时,发电机线圈温度、铁芯温度无论是平均值,还是最大值均在标准范围。机组在110MW能够安全稳定运行。
6 结论
改造后消除原机组存在的弊端,提高了机组出力,并可以在110MW工况下安全连续运行,发电机各项指标无任何超标现象,调速系统DEH改造达到了改造要求,完全达到了现代化设计的机组标准,提高了机组使用寿命和机组自动化水平,为国内同类型机组改造提供了很好借鉴。 ——此文章转载于互联网,文中观点与本网站无关,如有侵权请联系删除
100MW汽轮机通流技术改造及应用
- 发布时间:
- 来源:机电之家
关于阿里巴巴国际站
阿里巴巴国际站成立于1999年,是阿里巴巴集团的第一个业务板块,现已成为全球数字化出海服务平台。阿里巴巴国际站累计服务200余个国家和地区的超过2600万活跃企业买家,近三年支付买家的复合增长超过100%。
阿里巴巴国际站致力于让所有的中小企业成为跨国公司。打造更公平、绿色、可持续的贸易规则。提供更简单、可信、有保障的生意平台。它始终以创新技术为内核,高效链接生意全链路,用数字能力普惠广大外贸中小企业,加速全球贸易行业数字化转型升级。
未来三年,阿里巴巴国际站将赋能全球3000万活跃中小企业,实现全面无纸化出口、货通全球。
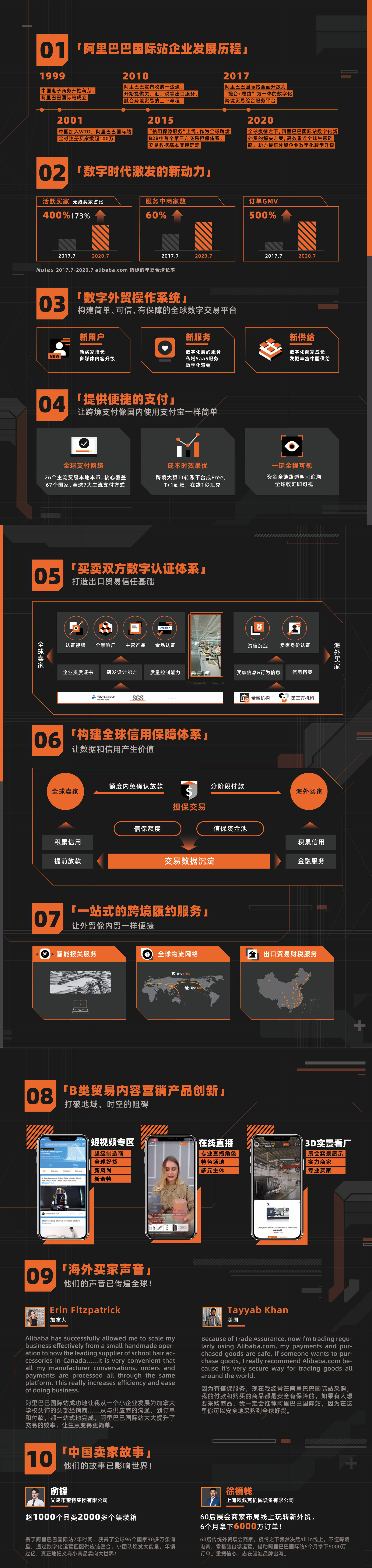